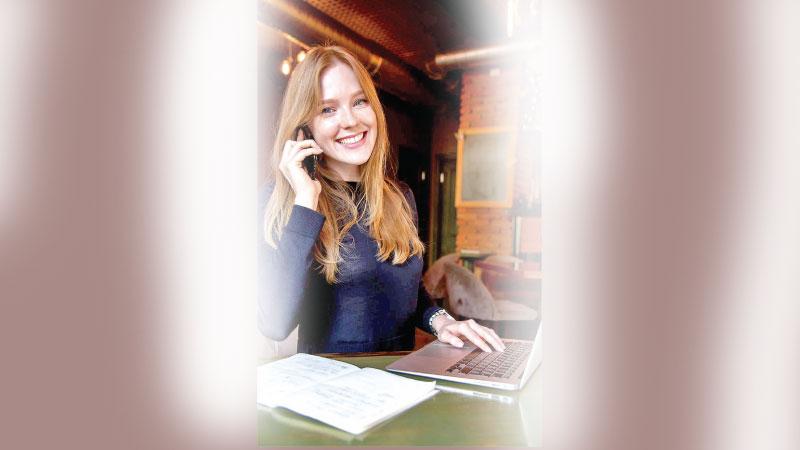
When the 5S system was first introduced to Sri Lanka in 2002, it was accepted by persons and organisations enthusiastically. However, Sri Lankans have a tendency to forget positive innovations easily. As a result, some people even do not know the meaning of 5S after two decades of its introduction.
The message of 5S is quite sound. If you adopt it, you will live in an orderly and clutter-free environment. It also created a mini-revolution by setting standards to organisational and management aspects of companies. Although 5S received positive responses when it was introduced, organisations and persons seem to have forgotten its real value. They may have done so consciously or unconsciously, but the fact remains that 5S is necessary for developing countries such as Sri Lanka.
The 5S system should start with schools. Although schools in remote areas may not have the infrastructure facilities, 5S would give them a sense of discipline. Before introducing 5S to schools, it should be properly understood by the authorities. If you take only the surface value of the 5S system, you will miss its deep philosophical aspects.
The 5S system consists of five steps. The first step is to remove unwanted items from your environment. When it was first introduced to us on December 28, 2002, we started removing unwanted items from homes and workplaces. Whether we are following that system today is questionable. When you remove unwanted items, you will save space in your houses and workplaces creating a pleasant atmosphere. When you work in such an environment, you will not be subject to mental stress. When the environment gets cluttered, even your mind will go haywire.
For many people, removing unwanted items poses a problem. Therefore, you should classify and sort out everything around you. Some of the items may be broken, outdated or rendered useless. They can either be discarded or sold. If you think that a particular item may be required later, you may store it in the attic without keeping it in your office or bedroom. There are certain items you require occasionally. One such item is the big bronze lamp which takes the centrestage on the New Year day. Even that can be stored away. If you require a certain item regularly, such as the razor, keep it in the bathroom.
When the 5S was introduced two decades ago, we used to have a big cleaning day at home or in the workplace. On that day, we cleaned all rooms, removed cobwebs and dusted the furniture. We encouraged children to clean their desks and keep the books neatly. When you separate items into several categories, you will be able to dispose of them easily. After the initial clean-up program, formulate a method for regular disposal of clutter.
Visual control
Step two of 5S requires you to designate a place for everything you handle. You should have a permanent place to keep your glasses, bunch of keys or mobile phone. Otherwise you will waste a lot of your precious time to locate them in the morning.
You should be able to locate anything within ten seconds and return it to its designated place. When 5S was in full swing, many organisations numbered their rooms and ensured proper lighting and ventilation. Some companies put up direction boards. Even an ordinary mechanic can adopt a colour code for easy identification of his tools. When you have visual control of everything, you can perform any task properly.
The third step is to maintain a clean workplace. Although most private organisations keep their buildings and premises clean and tidy, the situation in some government departments is far from satisfactory. When it comes to cleaning the office and premises, all the employees from top to bottom should take part in it. The same situation prevails in houses. Grandparents, parents, children and those who are hired to work should take part in the cleaning process.
The fourth step is to set standards. The aim is to maintain an environment where all the first three 5S are implemented. Standardising can be extended to other areas such as drafting letters, referring to international time or numbering the furniture. Such activities will help you to have a visual control of the whole place. Even tables, chairs, cupboards and dustbins should be standardised. You can use colour coding for locks for easy identification.
The fifth step pertains to training and disciplining the staff. No organisation can prosper without a trained and disciplined workforce. If workers are not excited to work in a particular organisation, there is something wrong with the system. Therefore, we should educate everybody on the significance of 5S. In the past, there were 5S slogan competitions in certain organisations. If you can create a 5S culture, everyone will work happily. The management has to motivate the workforce from time to time. A reward scheme should be introduced for better results.
The 5S system began as part of the Toyota Production System. The manufacturing method was initiated by the leaders at the Toyota Motor Company in the early and mid-20th century. The system, often referred to as Lean manufacturing in the West, aims to increase the value of products or services for customers. This is often accompanied by finding and eliminating waste from the production processes.
The 5S system is not just a methodology, but a culture that has to be built into any organisation which aims for spontaneous and continuous improvement of the working environment. The system involves everyone in the organisation.
The philosophy
The Japanese developed the simple and easy words religiously and practised the philosophy of 5S in every aspect of their lives making it a worldwide system.
Adopting the 5S system effectively at home can be a challenging task. Those who understand its significance will try to dispose of clutter. However, there are housewives and retired people who will object to the removal of many items for sentimental reasons.
There are mothers and grandmothers who still keep their children’s and grandchildren’s toys and used clothes for sentimental reasons. Most Sri Lankans have been brought up in such a culture.
To change the system, 5S should be introduced to young children.
Many organisations that embraced the 5S system seem to have given it up.
The coding system is no longer in force in certain organisations. They may not have understood the philosophy behind the 5S system.
To increase productivity, the 5S system provides guidelines. When workers are satisfied with the working environment, their productivity will increase.
Unlike Information Technology, the 5S system encourages workers to become active players in the company’s progress.