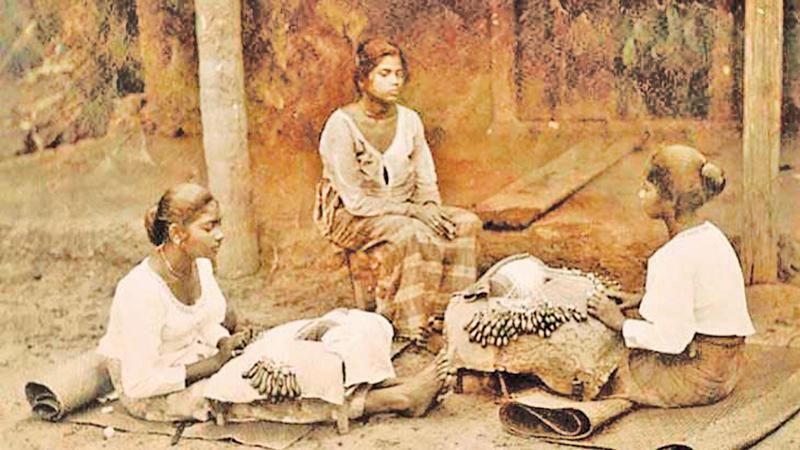
There are many traditional industries that can be found in almost every part of Sri Lanka. These industries, which have been run by households in the past, have since adapted to the modern world.
Among the oldest traditional industries in the country, the art of spinning Beeralu Lace has a significant place. This industry is found in many parts of the Galle District of the Southern Province and is a popular industry locally and internationally. There is a high demand for Beeralu Lace both in the local and international market.
Unfortunately, many people are reluctant to join the industry due to certain issues that have arisen in the Beeralu Lace industry at present. However, one would be surprised to know that the rural women of Galle, who in the past excelled in the art of Beer Lace, have even exhibited their products in countries such as the United Kingdom (UK) and Germany.
Beginning
When studying the origins of the Beer Lace industry, it is appropriate to focus on the production of cotton yarn used for this purpose. According to the story of Vijaya-Kuveni in the Mahavamsa, Kuveni was spinning cotton in the guise of a hermit and it appears that cotton cultivation had spread in the northern part of the island at that time.
In addition, the cultivation of cotton in the southern part of Ceylon is confirmed by the stories of the Riddi Yagaya or Rata Yakuma Shantikarma in which the seven Riddi queens arrived at Ussangoda, cultivated chenas, sowed cotton, prepared a cloth and offered it to Deepankara Buddha. This indicates that cotton cultivation and related products have been a traditional industry in the country for centuries.
Dutch
According to records, the Dutch were also interested in cotton cultivation during the colonial period. Especially after the Dutch established their dominance in the country in the 17th century, it seems that they, unlike the Portuguese, were constantly interested in dealing with the natives. As the port of Galle was a major harbour in the island at that time, they maintained close ties with the surrounding villages.
It is believed that as a result of their visit to villages such as Magalle around Galle for various activities, women in the coastal areas learnt from the Dutch and became accustomed to spinning Beeralu Lace. The fact that the Beeralu Lace weaving technology is still in use in the Netherlands and Belgium is a testament to the fact that it was introduced to Ceylon by the Dutch.
Another legend
Although folklore tells a different story about the origins of the Beeralu Lace industry than the above, it seems to be a mere myth. According to them, Kuveni was saddened by the fact that the women who lived along the southern coast at that time covered their body with only a cloth up to the breast area and she then turned a rock on a shallow beach in the Midigama area near Ahangama into a Beeralu Pillow (a part of the equipment needed for the Beeralu Lace industry) and taught the women in the area to knit jackets. This rock is still known as ‘Yakinige Kottaya’.
Distribution
The Beeralu Lace industry, which was earlier a domestic industry, became a commercial industry in the late 19th and early 20th centuries, and by the 1970s there was a high demand for these products from foreigners. According to the sources, the art of Beeralu Lace first originated in the Galle area and later spread to Weligama, Kathaluwa, Dodanduwa, Ambalangoda and Dondra.
There are three main types of lace in the world, of which the lace is made using a Beeralu Pillow, the Tatin Lace with a Tatin Shell, and the hand lace with wool. All three types of lace are currently manufactured in Sri Lanka, but Beeralu Lace is in high demand due to their uniqueness and beauty.
Raw materials
The main raw material used in the manufacture of Beeralu Lace are plain white cotton yarn, and today shiny gold and silver yarn is also used. In the past, cotton was particularly made into yarn for this purpose, but today, normal spinning cotton is used. In addition, the Beeralu Pillow is one of the main tools used for knitting Beeralu Lace. This consists of two parts, the lower part is called the pillow and the upper part is called Isbissala or Koiruwa. These are made by filling a frame made of sturdy wood with straw.
Beeralu are another important part of this industry. The use of these Beeralu is also the reason for the use of the name ‘Beeralu Lace’. Guava, Atteriya and coconut are the most widely used wood for making these Beeralus. In addition, in the past, wealthy women used Beeralus made of expensive wood such as ebony, and ivory.
Kotukolaya and pins are two other main tools used in knitting. The Kotukolaya is used to mark the pattern to be knitted first, and the pattern is dotted with a pen or pencil where needed. When knitting, pins are used to hold it in place to prevent the pattern from moving.
Craftswomen
In the early days this industry was done as a domestic industry. Although most of them practised the industry from mother to daughter, later on due to the high demand for these products, experienced women in rural areas started centres and taught Beeralu Lace industry. Several artistes who have made a significant contribution to the art of Beeralu Lace can be found in the Magalle area of Galle.
Carolinehami, a talented lace maker from Magalle, hosted a lace exhibition in 1906 in Alcott, London, at the invitation of a British national named John. She was pregnant at that time and gave birth in a London hospital. The baby was named P.K. Babynona and she was the first Ceylonese to be born in London. Since she was born in London, the villagers called her Londonhami. Due to Carolinehami’s talent at the said exhibition, she had also had the opportunity to meet the then King of Britain. Londonhami alias P.K. Babynona also excelled in Beeralu Lace and she also held an exhibition in Berlin, Germany.
Ratnawathie sisters
Sisters Somawathie and Ratnawathie can be introduced as two other women who took the industry forward after Carolinehami. Somawathie taught many young women to knit lace by establishing a centre and these sisters were also the first lace craftswomen of ‘Laksala’ which was started in 1964 under the then Sirimavo Bandaranaike- Government. Somawathie also designed the lace for the wedding dress of Princess Diana at the Charles-Diana wedding in 1981.
B.P. Alice Nona alias Sudda Nona, a descendant of the first generation to excel in the Beeralu Lace industry, was accustomed to knitting with her grandmother. Her grandfather and father made a living by selling ebony and turtle shell carvings to foreign tourists visiting the port of Galle, and they also sold Alice Nona and her grandmother’s Beeralu Lace to foreigners.
Following her marriage, she sold her products to British Royal Army Officers at the Koggala Air Force Base during World War II. As a result of this thriving business, she had also opened a shop called ‘Britannia Stores’ at the Katunayake Airport.
Teaching
It is said that the British Royal Air Force Officers bought a large quantity of lace there. She later opened stores at hotels in Boosa, Bentota and Hikkaduwa and was a leading lace designer and supplier at Laksala.
She was a founding member of the National Crafts Council, which started in 1982, and has taught more than 200 women to knit through Laksala and the National Crafts Council. She can also be described as the first Beeralu Lace businesswoman in Sri Lanka. In 1992, then President R. Premadasa presented the ‘Sri Lanka Thilaka’ Presidential Honorary Award to Alice Nona in recognition of her service to the arts.
New trends
The interest of the new generation of fashion designers in these products, the re-emergence of lace-related designs and the research done by various parties have contributed to some advancement in the art of Beeralu Lace today. These days, Beeralu Lace weaving can also be seen live in hotels and jewellery stores visited by foreign tourists.
Exhibitions sponsored by Government and Non-Governmental Organisations can also be seen to promote the industry.
However, one of the major problems associated with this industry is that the middlemen make huge profits and the designers do not get a fair price for their products due to the lack of proper places for them to trade.