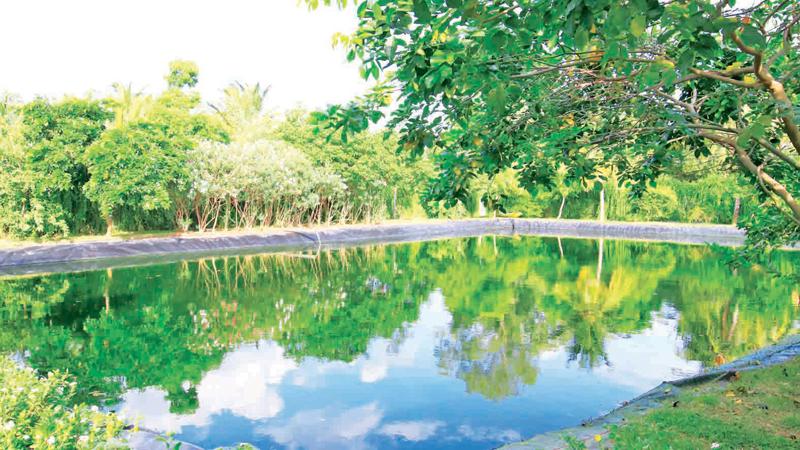
Brandix, a billion dollar apparel entity, aims at achieving hundred percent carbon neutrality by 2023 in its quest towards recording a zero carbon footprint and setting a benchmark in the country’s manufacturing sector.
The company has invested US$ 28 million under a five-year strategic plan to achieve this ambitious goal at its factory in Batticaloa. Its decarburisation strategy involves on-site renewable energy generation, the addition of nearly 20MW of solar and biomass to its current energy mix and resource optimisation strategies with installation of technologically advanced and energy efficient air compressors, HVAC systems, sewing machines, lighting and building fabric.
“We have also invested around US$ 13 million on solar panels which will help us reduce carbon footprint and achieve our long term objective of fully neutralizing the impact on the environment from carbon dioxide emissions,” Brandix, Senior General Manager, Special Projects, Heminda Jayawardane said during a factory visit to the Brandix Batticaloa facility last week. The factory notched the world’s first Net Zero Carbon status this year.
The installation of a 1.65MW rooftop solar plant at the Batticaloa factory was initially Sri country’s largest solar installation. The 2,975 MWh annual energy yield exceeds the annual energy requirement of the premises.
![]() The production floor
|
Recognised by the World Green Building Council (WGBC), the ‘Net Zero Carbon’ certification is issued by the Leonardo Academy and comes in the background of countries around the world examining ways in which to minimize their contribution towards drastic climate change.
Since embarking on its sustainability journey in 2007, Brandix has achieved many milestones including securing the world’s first LEED Platinium certification in 2008.
“It is truly a monumental milestone for us to secure another world first by achieving net zero carbon status for the Batticalo factory to join in the World Green Building Council’s Commitment,” Brandix Director Projects, Natasha Boralessa. Adding that Brandix has signed up with the US Green Building Council for all Brandix facilities to achieve net zero carbon emission by 2023.
The company employs over 43,000 associates supported by 38 manufacturing facilities in Sri Lanka, India and Bangladesh.
The Group provides over 50 percent of value addition locally through its backward-linked operations in textiles, threat, buttons and hangers. A peek into an exclusive portfolio reveals Victoria’s Secret, Gap, Next and Marks and Spencer.
The company specialises in causal bottoms, intimate and active wear, woven and knitted fabrics and a host of apparel industry accessories.
Brandix launched its sustainability program focusing on minimising the negative impact of its operations on air, water and earth. Following the sustainability efforts the facility at Batticaloa has been able to slash carbon emission from 276.6g to around 56g to earn $1, water from 13.3 litres to 9.3 and diversion of 96 percent of around 80 percent water sent to landfill.
“We have invested around US$ 1.5 million on a biomass project to put an halt to the use of the costly and hazardous fossil fuels,” Brandix, Deputy General Manager Environmental Engineering, Jarook Mohamed said.
The building is designed according to US Green Building Council and ASHRAE (American Society of Heating, Refrigerating and Air-Conditioning Engineers) building guidelines.
“Around 44 percent of energy is consumed for the cooling of the building, hence we focused on optimising the cooling energy through the building design itself,” Mohamed said.
The East-West orientation of this building minimises the solar heat emitting through the walls and windows. The solar panels also provide additional insulation to the roof.
“At Brandix, we monitor Real Time Building Energy Consumption with the support of a Building Management System. HVAC air cooling and indoor air quality is continuously monitored and controlled, with a special focus on temperature and CO2 levels. Chillers and Air Handling Units (AHU) can also be operated and controlled through the BMS system. Advanced sub metering devices have also been provided to monitor daily energy consumption patterns,” Mohamed said.
The Batticaloa factory comprises 1,800 sewing machines which are operational for 16 hours every day. All machines are provided with low powered VSD Servo motors instead of Clutch motors. Clutch Motors are continuously operational during production hours, whereas Servo Motors operate only during needle time, which accounts for approximately 17% of operation hours. A Servo motor can save 68-73% of energy when compared with a Clutch motor.
Knitted garments need uncurling as part of a new operation requirement. For this purpose, compressed air is used continuously. The in-house team then went onto develop an innovative air saving device to reduce the compressed air wastage by over 40%. We will be implementing this device across new sewing machines as well.
Around 11 percent of energy is used for the building’s lighting. Solar tubes provide solar light into the building minus the solar heat. The factory lighting is 100% LED generated as LED consumes less power than CFL, resulting in savings of over 50% lighting energy load versus conventional lighting.
The lifetime of LED lighting is also double the span of conventional lighting. LED lighting can also be easily recycled and completely eliminates any disposal issues. “We segregate and store used thread cones in separate bins. These threads are then re-used when new styles are introduced. All solid waste is segregated and stored in separate bins for recycling. In-house water purification system provides safe drinking water to all our Associates,” Mohamed said adding that treated water is recycled and re-used for flushing and irrigation purposes. The response of employees towards achieving carbon neutral status according to officials has been encouraging.
“We have received the fullest support of employees who have realized the importance of minimising waste and its impact on the environment. They have been cooperative and supportive in adopting and adhering to new processes and practices,” Group Head of Engineering, Iresha Somarathna said. Over 140 employees of the Batticaloa factory are ex LTTE combatants who have been fully rehabilitated and re-integrated to society.
“This is the number that we know. There may be much more employees who had been former carders but the fact is that they are good workers contributing to the growth of the company,” an official of the Batticaloa factory said.
Brandix through its Corporate Social Responsibility initiatives has provided drinking water facilities to families of employees, religious and educational institutions in the location.
Brandix, Head of Corporate Social Responsibility, Anusha Alles said employees and the vicinity they live in, are central to our organisation. Health and education play a pivotal part in their journey and it is when these needs are addressed that an organization gain and the society benefits.